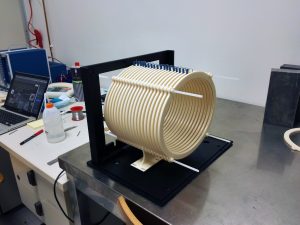
At the beginning of 2017 a new instrument – on the cutting edge of 3D Printing – started to operate in our Labs. Three printers, two complementary technologies and more than 15 different materials to build prototypes or components intended for direct use are now available at Servizio Progettazione e Costruzioni Meccaniche of Technical Division.
Fused Deposition Modeling (FDM) is a revolutionary alternative to traditional manufacturing of single components and/or mechanical systems made of engineering-grade thermoplastics, offering designers an extraordinary freedom of shaping, together with a very good mechanical and thermal behavior of the printed object. Today, the Service specialized technical staff is fully trained to operate on two of the most advanced systems on the market. In five months of activity more than 15.000 cm3 of material have been printed in more than 1000 hours of printing, serving several INFN experiments.
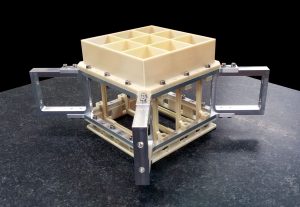
The 3D technology available at LNF is the easiest and fastest way of prototyping with the ultimate precision and versatility. The process jets and solidifies thin layers of liquid photopolymers – using the energy of a Ultra Violet light beam – and it is capable of printing parts in 16-micron layers and in multiple durometers. You can print transparent, opaque, rigid and flexible materials. The printer is normally used in industry to realize demonstration models, but more and more often, at INFN, the aim is the direct use of the printed product, when high precision or transparency, rather than the durability of the printed part, is required.
Translation by Camilla Paola Maglione, Communications Office INFN-LNF