The testing of the first prototype of the plasma accelerating module of the EuPRAXIA @ SPARC_LAB project has been successfully carried out in the Plasma_LAB laboratory.
. Unlike the previous tests, which were performed with discharge capillaries of a few cm in length, in this case it has been demonstrated the possibility of creating a capillary of nominal length, 400 mm as foreseen in the Conceptual Design Report of the project, capable of supporting a uniform discharge along the entire structure.
The EuPRAXIA@SPARC_LAB project, intended to put forward LNF as host of the EuPRAXIA European Facility and recently included in ESFRI (European Strategy Forum on Research Infrastructures), provides, for an electron beam injected into the plasma at 500 MeV, the achievement of a final energy of 1.1 GeV through the use of a plasma section capable of ensuring an accelerating gradient of 1.5 GV/m.
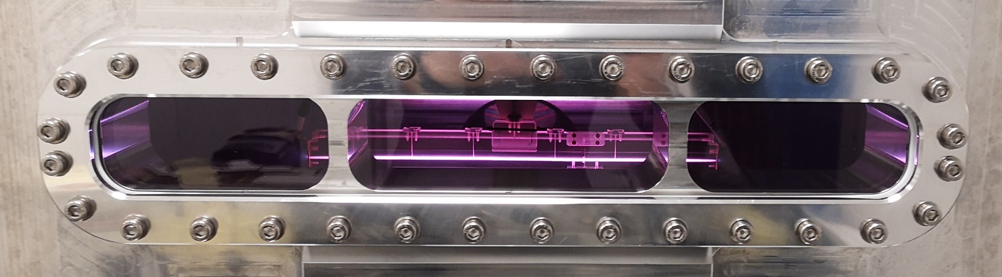
During these first tests, a stable and reproducible plasma with an electron density of the order of 1016 cm-3 has been created and confined within a capillary 400 mm in length and 2 mm in diameter. The plasma source has been entirely designed and built at the LNF.
The plasma formation technique is based on the use of high-voltage pulses (between 10 and 25 kV, with current peaks up to 2 kA and duration around 600 ns) to ionize a homogeneous gaseous hydrogen column produced between two electrodes.
The synchronization between the gas injection into the longitudinal capillary’s channel, obtained by means of 6 vertical inlets, and the instant for supplying the high-voltage pulse represents a crucial point to achieve stable and uniform plasmas suitable for producing high-quality accelerated beams.
Given the considerable size of the plasma source and the impossibility of making it in a single piece by using common 3D-printers, two sections are printed and then later joined by means of a die-casting technique, which provides gas losses of the order of 10-10 mbar.
The systematic characterization of the plasma behavior during the gas discharge has just begun, but its first ignition represents a very important milestone for the EuPRAXIA project and in any case a novelty on the world scene.